 |
|
 |
 |
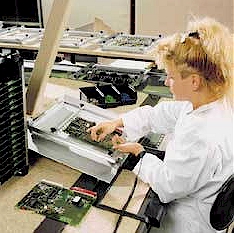 Quality Improvement
Psychonomics works with clients for a viable solution that will improve quality in products or services. Quality interventions we recommend are relevant to a variety of situations, such as those where organizations are experiencing:
 | New technologies |
 | Changes in workforce strength |
 | Absenteeism |
 | New market opportunities |
 | Repeated production problems |
 | Errors |
 | Accidents |
 | Competition |
 | New work practices |
|
Psychonomics is very aware of the fact that under all these conditions the intervention or program we recommend needs to be fully integrated in terms of service formulation or production. Indeed, when new work practices are required, quality becomes even more of an issue as it must be built into the production process rather than just being something that is done at the end. And inasmuch as this is true, we also strive to make sure that besides employees, the wider inputs to quality, such as outside contractors and suppliers, are all taking responsibility at the appropriate level.
In addition, when it comes to issues of quality, we are very aware of the need for organizations to retain core, skilled personnel, as well as be ready to change orientation when the situation, or the market, alters. However, questions we often face when circumstances change include, are there enough employees to do the same high-quality job? And, how have these personnel coped with the requirements of new technology? In many instances, employees suddenly find themselves with a lot more work and responsibility, often for the same pay, and management have not taken this into account.
After extensively assessing the need, Psychonomics will often implement quality systems that include more than one type of element. For example: Quality control, quality assurance, quality standards, and total quality management systems (TQM). These center on products, processes, procedures and employees, respectively - all are required, to some degree, for a large-scale operation to be effective. It should be borne in mind, though, that none of these methods are perfect and we take extreme care in their use, and always within the context of the overall organizational picture. Furthermore, when the elements are already present in the organization, they can be the source or very specific problems, as outlined below, which we seek to address with clients. Certainly, if your organization has stressed one element at the expense of another this can lead to major problems occurring.
|
Quality Control:
This method is basically a sieve where something is made, and if it is good it is kept and if it is bad it is thrown away. Very necessary, but often this method doesn't get to the root of any big problem. Other difficulties can occur as a result of the language and culture that develops around the quality control initiatives, what can be termed in the UK as 'ISO speak'…!
Quality Assurance:
Something is made or a service provided and then checked - either using a measure or the complaints record is analyzed. This approach can work well, but it can be limited as it looks only at the process itself to eradicate the problem (including training, machinery, raw materials), and usually after the process has finished to produce the product or service. It doesn't address organizational factors or any cultural problems that might be the root cause. For example poor communication between departments.
Quality Standards:
The goal, objective, target, or even checklist is centered at lower-employee levels, and usually conducted during the production process, service delivery, or it is ongoing. The method is useful but working to only the level of a standard gives rise to the notion that as long as the standard is met the job has been done properly. This has radical implications for safety. Furthermore, when the system is overly centered on targets or metrics, the company can lose its way and progress and development are threatened - the purpose becomes the target! Perhaps the worst result of this, though, is where a lack of planning is covered with a veneer of activity and there is an illusion of achieving things. Similarly, when this happens rather than letting personnel get on with their work, the organization has become a controlling entity that distracts from the real purpose.
TQM:
This is a method of improving quality whereby responsibility is placed into the hands of employees to a greater extent. The rationale here is that the organization's employees are the people who do the job and are really the experts. If there is something wrong in the company - or there is a particular problem that needs addressing - they are the best placed to identify it and put it right.
One of the best known methods of utilizing employee knowledge that we may implement is the quality circle. These are self orienting or self directed groups that provide the opportunity for individuals to participate in decisions about tasks and products or service improvements. They can also boost morale and impact on the quality of employees' working life.
Throughout any TQM implementation, Psychonomics works to increase involvement of employees, enhance business effectiveness, as well as using the quality circle as a vehicle for any required organizational culture change. These systems are, in fact, sometimes initiated by a realization that poor quality in performance may be a result of current job design; the end result being that the product made might not be up to a comparable standard to the competition, as a result of the way task elements to make the product are organized or checked. Hence, the method also provides an excellent starting point for us to help clients redefine work practices, needed competencies, and job specifications.
Besides quality circles, Psychonomics also implements several other support initiatives that include critical incident analysis, and sensitivity training. And from our perspective support is often key. For example, in order for TQM to work, employees must feel committed. To develop commitment we take a quality of working life (QWL) approach which seeks to make working life more meaningful, with jobs being more satisfying, involving and participatory, and to which employees can make a contribution. It is also a philosophy where people are viewed as assets rather that costs, having knowledge, skills, experience etc. Within this context Psychonomics may also seek to provide employees with greater empowerment by implementing methods such as semi-autonomous work groups and flexible work patterns.
|
|
Of course, personal views, power patterns, relationships, group sentiments, norms, perceptions of trust, feelings, needs, and desires, all play their part too in quality issues. And as far as management are concerned, it has been said - only half tongue-in-cheek - that problems with quality are a result of the pressure to have half as many people, paid twice as well, producing three times as much! Put another way, quality concerns often surface because there is a discrepancy between what people are doing and what other people think they should be doing. The question for us at Psychonomics is whether what they are doing is justified or not? And whatever level we find the root of the difficulty - be it at corporate, divisional, functional, task, group, or the individual level - the thrust of our approach is to always remember that at the heart of the current quality problem being experienced are processes or services that are controlled or delivered by real people, and that changes that have occurred may have done so for a very good reason. We aim to find out the real situation and then intervene to improve quality in the most effective manner.
|
|
 |
|
|
|
|